Na fabricación moderna, a aplicación deMáquinas de soldadura con láser de fibra 2000WPara a soldadura metais de aluminio está cada vez máis xeneralizada. Non obstante, para garantir a calidade e seguridade da soldadura, hai que destacar os seguintes cuestións clave.
1. Tratamento superficial antes da soldadura
A película de óxido na superficie do metal de aluminio pode afectar seriamente á calidade da soldadura. Debe realizarse un tratamento completo para eliminar a película de óxido, as manchas de aceite e outras impurezas. Cando unha determinada empresa de pezas de automoción soldou o marco de aluminio, debido ao descoido do tratamento superficial, apareceu un gran número de poros e fisuras na soldadura e a taxa de cualificación baixou drasticamente. Despois de mellorar o proceso de tratamento, a taxa de cualificación ascendeu a máis do 95%.
2. Selección de parámetros de soldadura apropiados
Os parámetros de soldadura como a potencia láser, a velocidade de soldadura e a posición de foco son de gran importancia. Para placas de aluminio cun grosor de 2 a 3 mm, é máis adecuado unha potencia de 1500 - 1800W; Para aqueles cun grosor de 3 a 5 mm, 1800 - 2000W é adecuado. A velocidade de soldadura debe coincidir coa potencia. Por exemplo, cando a potencia é de 1800W, unha velocidade de 5 a 7 mm/s é ideal. A posición de foco tamén afecta ao efecto de soldadura. O foco para placas finas está na superficie, mentres que para placas grosas, ten que ser máis profundo dentro.
3. Control da entrada de calor
O metal de aluminio ten unha alta condutividade térmica e é propenso á perda de calor, o que afecta á penetración e á forza da soldadura. É necesario un control preciso da entrada de calor. Por exemplo, cando unha empresa aeroespacial soldada en aluminio soldada, o mal control da entrada de calor levou a unha fusión incompleta da soldadura. O problema resolveuse despois de optimizar o proceso.
4. Aplicación de gas de blindaje
O gas de blindaje adecuado pode evitar a oxidación e a porosidade da soldadura. O argón, o helio ou as súas mesturas úsanse comunmente, e o caudal e a dirección de soplado deben axustarse correctamente. A investigación demostra que un caudal de argón de 15 a 20 l/min e unha dirección de soplado adecuada poden reducir a porosidade.
No futuro, espérase que xurdan equipos de soldadura con láser máis elevados e intelixentes e que se produzan novos procesos e materiais de soldadura tamén promoverán a súa ampla aplicación. En conclusión, só seguindo estas precaucións, acumulando experiencia e optimizando o proceso poden exercer as vantaxes da soldadura por láser para contribuír ao desenvolvemento da industria manufactureira.
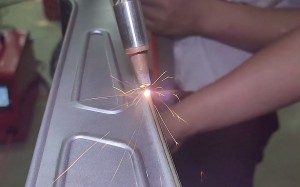
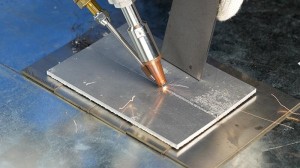
Tempo de publicación: xul-12-2024